Manchester Recycling Firm Saves £17k with CPM Smart Sensor Technology
Working with a Manchester Recycling Company, savings of £17,000 were achieved by detecting an impending failure on an electric motor as a result of installing CPM Engineering’s Smart Sensor technology.
The problem – the common cause, cost and inconvenience of motor failure
Dust and dirt contamination is a common cause of expensive motor failure in all types of industries, even on increased protection machines such as IP65 enclosures, which is why our client chose CPM Smart Sensor technology.
Examples of industries suffering such environmental challenges, who would benefit from CPM Smart Sensor technology, include food processing, chemicals, pharmaceuticals and, in this instance, recycling.
Dust can surround the motor or settle on the outside of machine enclosures in layers. The cumulative effect, in this particular example, was that a sudden build up of dust restricted the cooling system on the electric motor.
The result was an increase in the skin temperature which was detected by a CPM Smart Sensor that was fitted to the motor fins. This information was transmitted live from the Smart Sensor to CPM’s remote monitoring centre based in Trafford Park, Manchester.
Traditional ‘route based’ monitoring is typically performed every few weeks. Looking at parameters such as temperature, vibration and bearing conditions, it gives a ‘snapshot’ of the health of the machine.
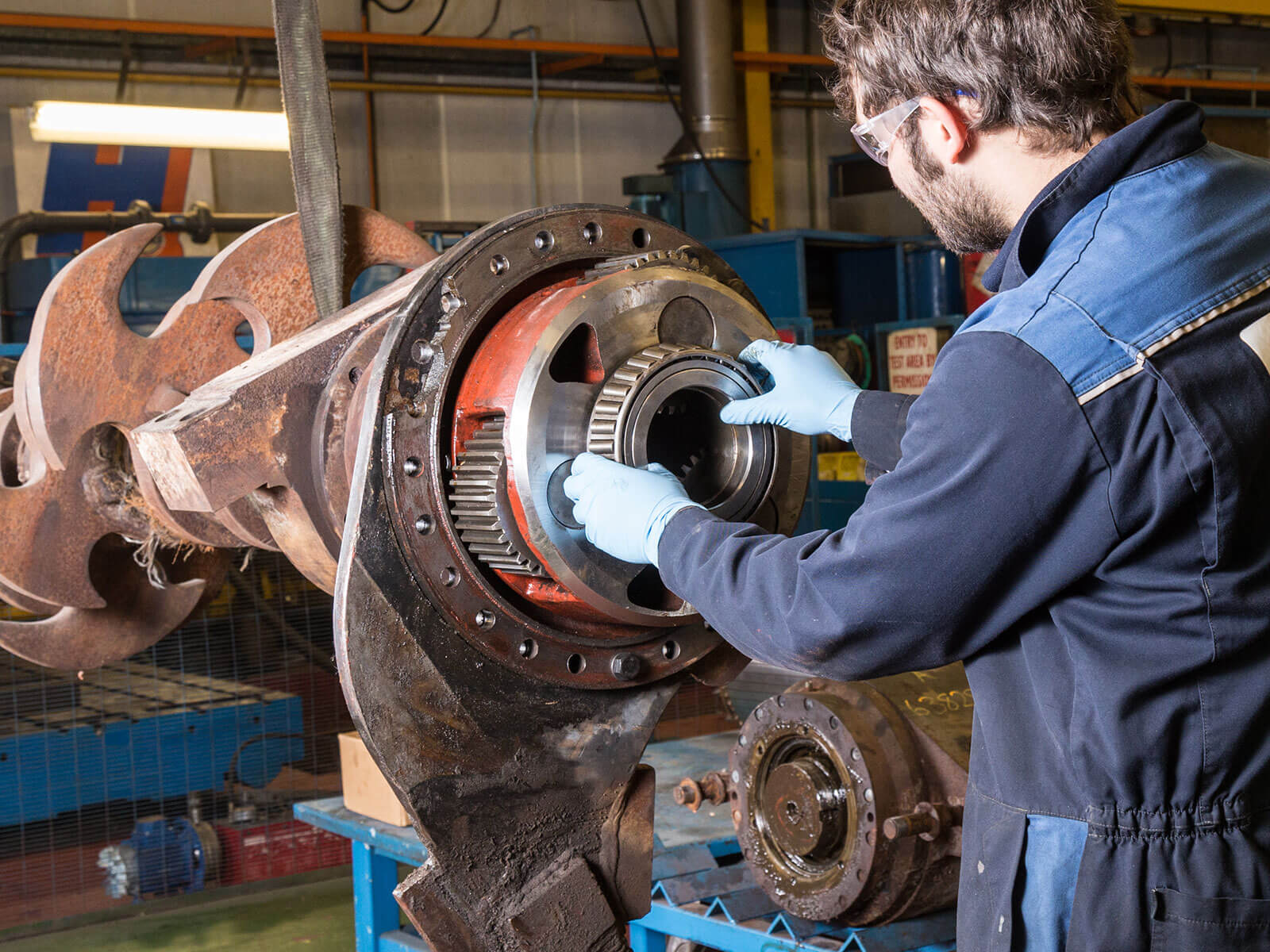
Issues often develop in between monitoring and are usually detected too late, resulting in failure and subsequent expensive downtime. Repairing the damage resulting from unplanned failures typically costs 3-4 times the cost of overhauling a machine.
In many instances, thousands of pounds are lost due to secondary damage caused by the initial failure. This was the danger faced by the Manchester Recycling Company – one of our CPM Smart Sensor partners.
The solution – the right information at the right time with CPM Smart Sensor technology
CPM Smart Sensor technology allowed for intervention at an early stage and before failure occurred. In this case, we saved our client £17k on a motor.
With dust particles quickly accumulating and covering the fan cowl, it was only a matter of time before one of the critical electric production motors would overheat. Had it overheated, which was an inevitability, it would have been an expensive fix for our client.
Smart Sensors are advanced warning systems. Using real time notifications of the motor’s high skin temperature and impending failure, the Smart Sensor automatically flags up the threat to a CPM Reliability Engineer.
Thanks to the Smart Sensor, CPM’s Engineer quickly alerted the client who then took immediate proactive action to quickly schedule a fan cowl clean and avoid motor failure.
They saved:
- £5k of production lost in the first hour
- £1k for every subsequent hour
- The cost of the impending repair
- The opportunity cost of other important maintenance work not carried out on other machines
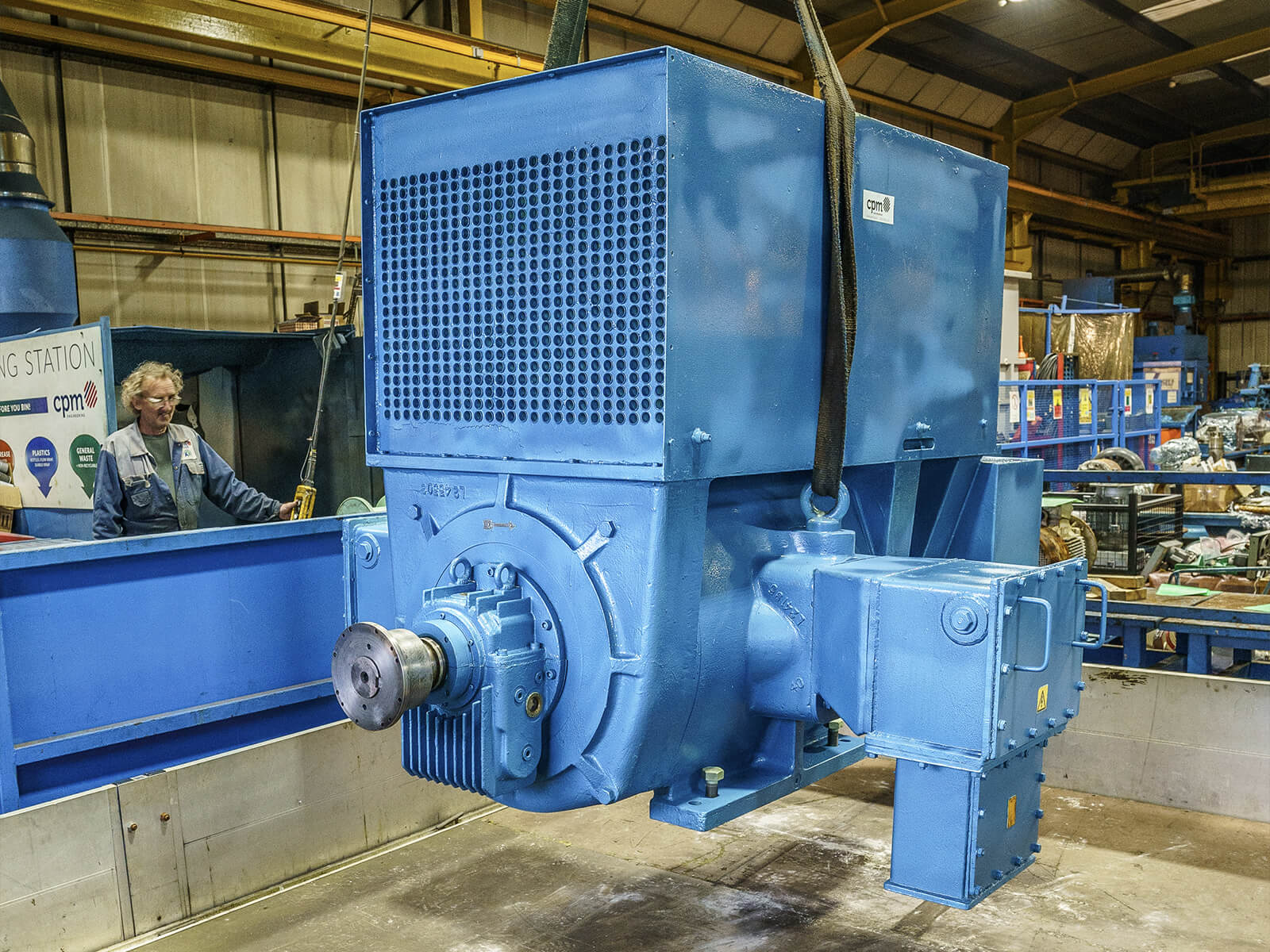
Still not convinced? Examine the data from CPM Smart Sensor Technology:
- 70% reduction in downtime
- Extend MTBF by 30%
- Improve energy consumption by 10%
Get in touch to secure your motors and your budgets
Want to learn more about how CPM Smart Sensors can radically reduce the cost and inconvenience of your motor failures? Contact our Team by emailing info@cpm-uk.com or calling 0161 865 6161.
You can also find out more about our ‘Pay as you go’ options, FREE Smart Sensor ‘proof of concept’ trials and fixed fee maintenance packages. We’re so confident in our Smart Sensor cost savings that we’ll GUARANTEE all motor maintenance at our own risk.