Predictive, Preventative and Reactive Maintenance of Motors
Post War and into the Industrial Age, Maintenance of Motors has become an important every day practice for most companies.
Initially maintenance was based around corrective actions, a “fix it when it broke” – reactive approach. From there an evolution in maintenance professionals have added more and more proactive elements to their maintenance strategy – preventative.
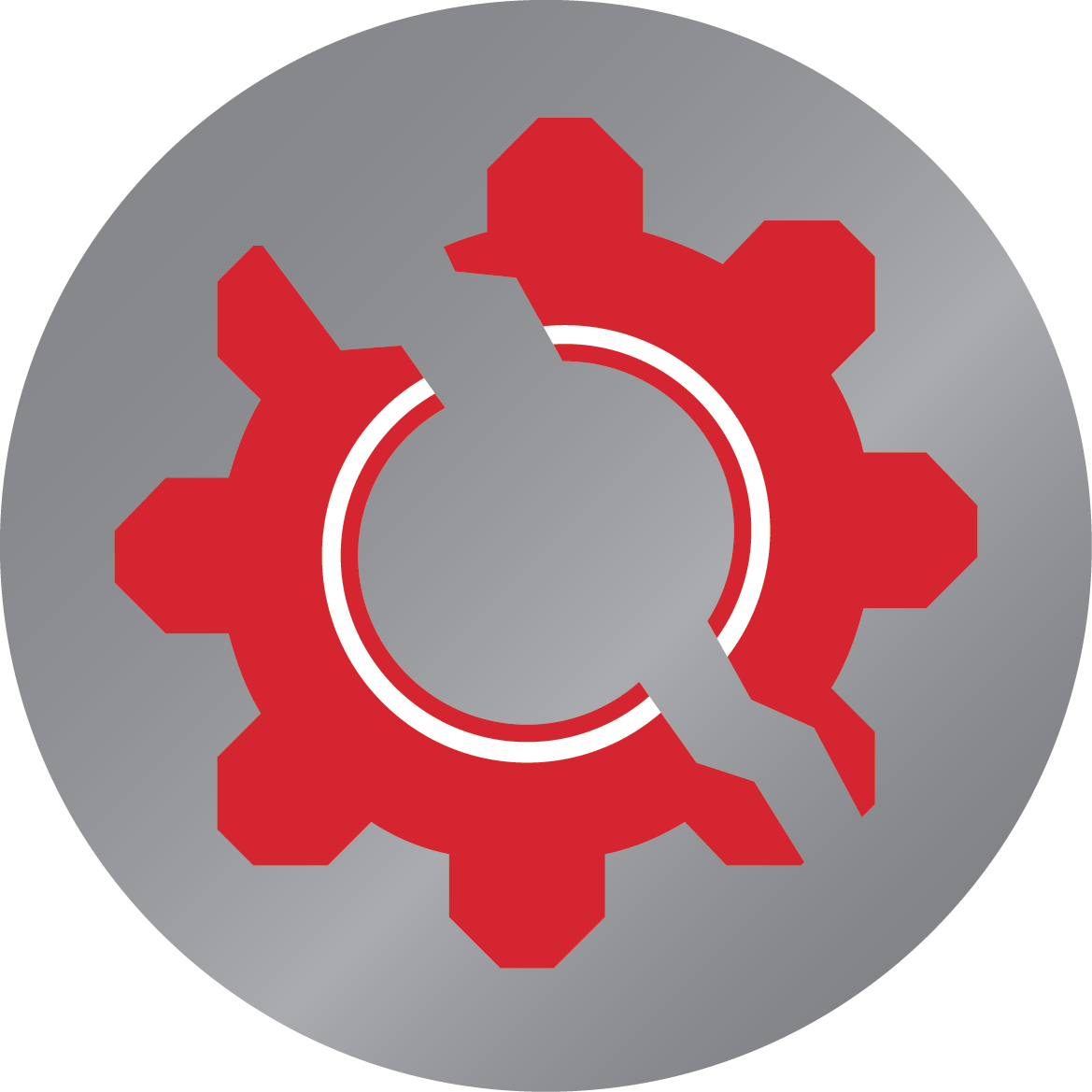
Post War
- Fix it when it broke
- Basic maintenance
- Corrective actions
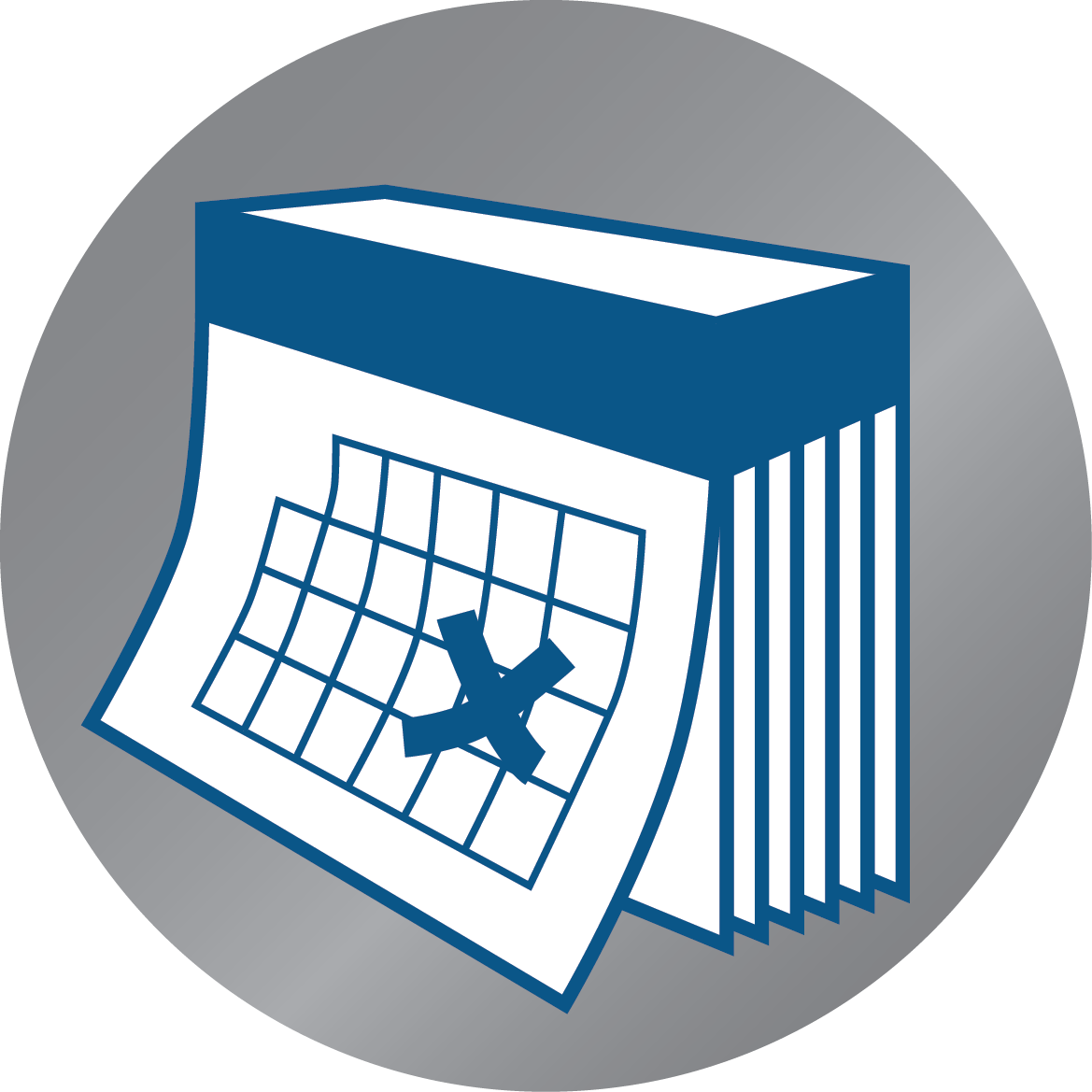
1955 – 1975
- Planned preventative maintenance
- Time based maintenance
- System for planning and controlling work
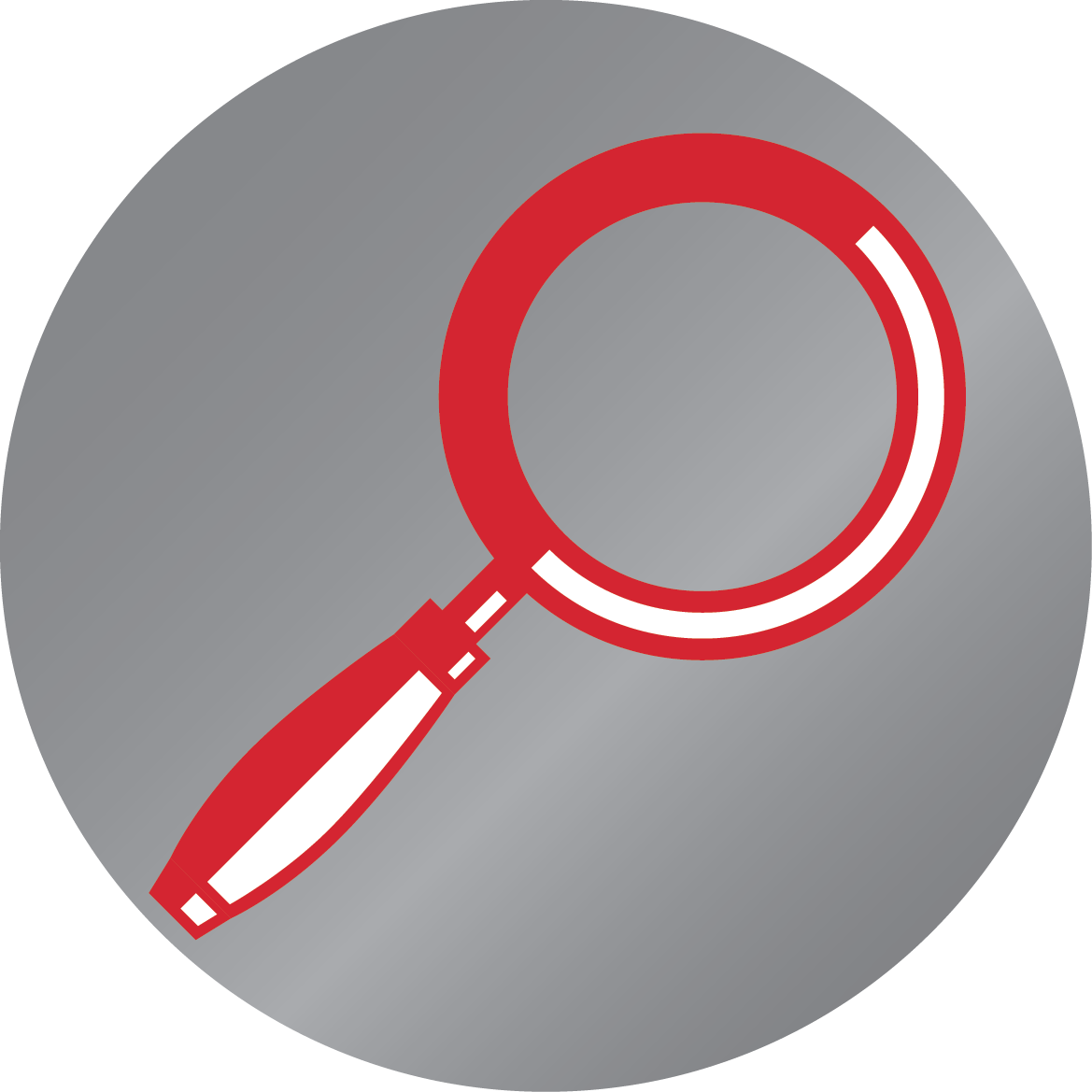
1975 – 2000
- Condition based maintenance
- Computer aided maintenance management and information system
- Workforce multi-skilling and teamworking
- Proactive and strategic thinking
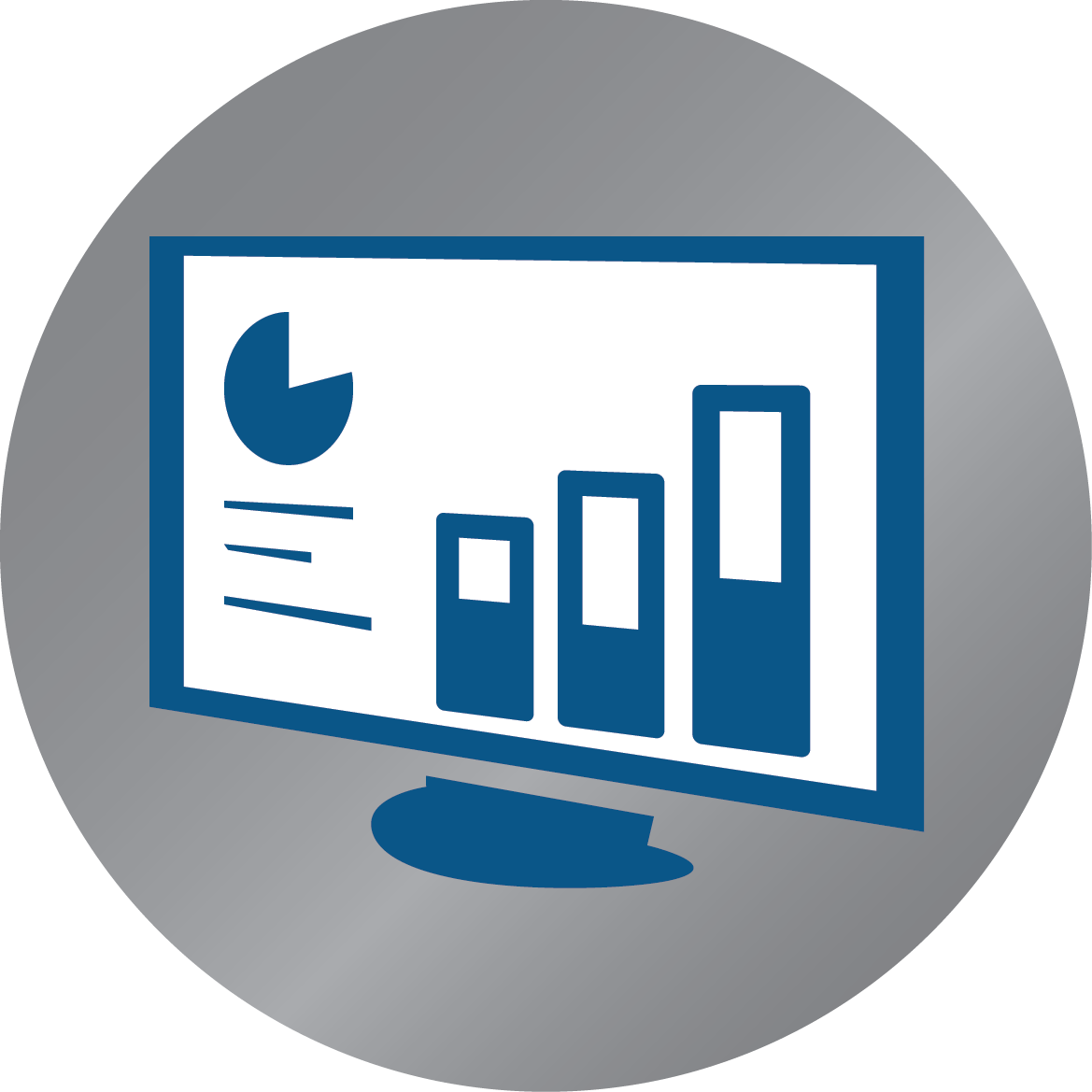
2000+
- Risk based inspection
- Risk based maintenance
- Risk based life assessment
- Reliability centered maintenance
- Condition based monitoring
- Computer aided maintenance management and information system
- IOT
Today, in leading companies, maintenance is seen as an integral part of business operations because it can have a significant impact on corporate profitability.
In a recent survey undertaken by our Trade Association, EASA on Time Devoted to Maintenance the results may be a little surprising.
Of the 3 maintenance strategies surveyed, Preventative, Predictive and Reactive, each member was asked to indicate the time devoted by maintenance staff to each strategy.
The 3 options being:
- largest proportion of time,
- second largest amount of time,
- smallest proportion of time.
What type of maintenance strategy do you spend the largest proportion of time on?
What type of maintenance strategy do you spend least time on?
Source: EASA 2014 maintenance practice study.
An amazing 60.5% of respondents spent most time on a reactive strategy.
Compared to 27.3% spending the largest time in Preventative maintenance and a very low 12.2% spending most time on predictive maintenance.
In contrast members spending the least amount of time on both reactive and preventative strategies was around the same level of 20%. A whopping 61% spend least time on a Predictive strategy.
Of course, there should never be a point where 100% is shown against any of the options below as there are many valid maintenance strategies available. They are not “right” or “wrong” but rather different approaches. Each organisation has widely different cultures, budgets, skills and opportunities in asset management and will need its own mix between the strategies.
However, what we are seeing is that those businesses who have evolved their maintenance systems have gone from being simply efficient towards achieving maintenance excellence.
With the advent of new technologies, the impact early detection can already bring and the fast pace that we now move at, the coming years bring exciting developments into predictive maintenance – continuing the change in perception that maintenance is an investment rather than a cost.
IOT. A fashion or a game changer?