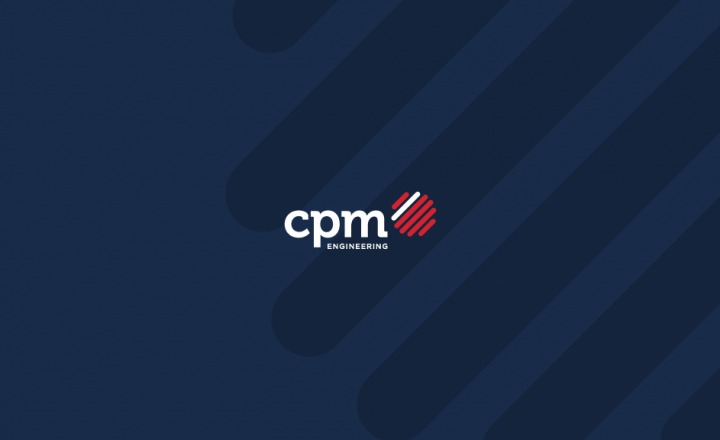
Case Study: Reducing downtime from days to minutes for client in food manufacturing industry
When our distressed customer came to us with an unexpected servo motor and gearbox breakdown, they weren’t just staring down the barrel. They were staring down three. With their entire production line out of action, no backup unit or spare parts and an estimated 16-week ’emergency’ replacement delivery, they were facing: £10k in lost production